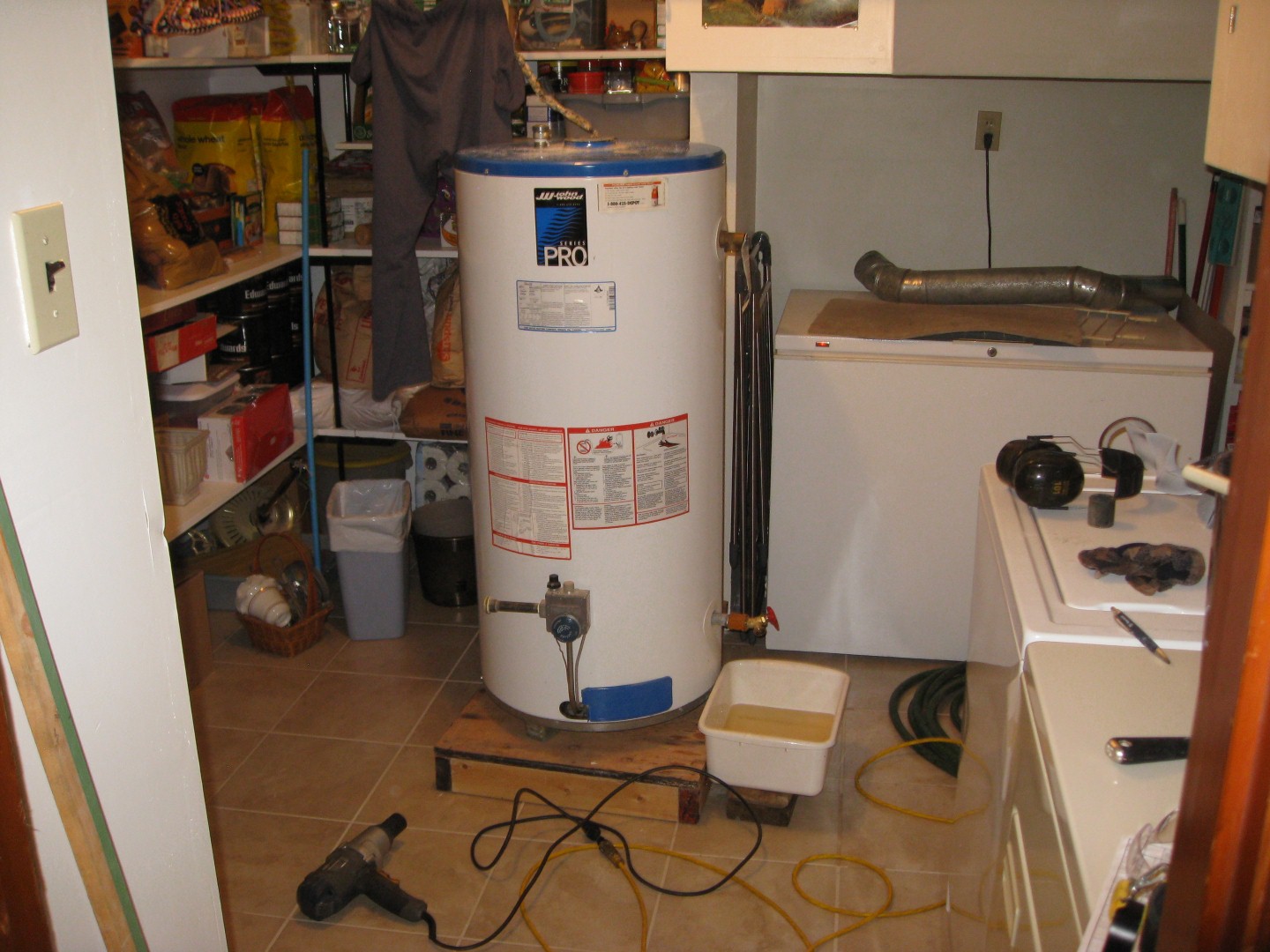
The Laundry Room Re-Visited
It’s been quite a while…. but I’ve returned to finish the job in the basement.
One of the nagging complaints about it was the still un-tiled portion of the laundry room, which was under the water tank and to the base of the furnace. It was one of those jobs that annoyed me every time I thought about it because tiling that portion of the floor was the easy part of the job.
Really, it was. I probably could have done this a long time ago (definitely), but a thousand bad excuses prevented me from doing so. Poor little me didn’t want to go without hot water for even a day (which was actually the extent of it), and I knew I’d have to turn off the gas to the tank… so I should wait until summer so the furnace isn’t needed, right?
What a putz….
Yeah, it wasn’t nearly as bad as I had made it out to be. I survived the water issue by filling several buckets with water prior to starting. I didn’t really need this as I actually had the cold water under pressure the entire time I was doing the job, but every time I used it water came out the open pipe over the tank and made a mess. For the one night without hot water, I had a “boat shower” – boiling water on the stove and mixing it in a basin – sitting on the edge of the tub, and that was that.
It also didn’t hurt to have Cassandra away for the weekend to lessen the paperwork from the complaint department…
So, enough of a prelude, on with the show.
The job in front of me was:
- Tile and grout the floor under the tank and to the furnace.
- Replace the dip-tube in tank.
- Replace the anode in tank.
- Rinse out the sediment from the tank.
- Replace and re-plumb the tank.
As you can see, the majority of the love went into the water tank. It had been in place for about a dozen years and had only been drained once. The manufacturer suggests draining it every 6 months (which I think is ridiculously frequent), and replacing the anode about every 5 years. Neither had been done, or done properly.
First thing was to remove the tank and get it into a workable situation. ** I took measurements of the inlet tube from the walls so I could replace the tank once I was done. ** I’ve taken out the laundry room sink to get access to the clean-out so I could drain the tank and move it. It weighs about 500 pounds full. I manhandled it up onto a little pedestal, and the impact gun was used to remove the anode… but I’ll get to that later.
As I said, tiling the floor was the relatively easy part. No, I’m not going to tile behind the damn furnace… just so it looks complete.
And while I was at it, I replaced some chipped tiles in the kitchen area.
Don’t go thinking you can get away with a steel weight set in a tiled area without dropping one sooner or later. It’s like have a new windshield installed. Just a matter of time…
That went really well once I learned to cut the grout out with a tile saw before chipping away at it. If you don’t, you pry up the tiles surrounding the busted one because they are “attached” via the grout. So I replace four instead of two…. learn learn learn.
I had a wet vac to suck up the dust as I cut, and the tiles chipped out with relative ease. A good cleaning of the surface, and it was good to go.
With both areas tiled, the glue had to set overnight, so it was time to get onto the water tank, and the first thing to do there was the dip-tube, which was easy to do because there was nothing left of it. The same could be said for the anode. The dip-tube directs cold water to the bottom of the tank so as to not mix fresh water with the hot water at the top, and the anode prevents the tank itself from rusting by “rusting” itself instead.
A sure sign dip-tube is NFG is that you only have about 10 minutes of hot water where you used to have all you needed. Mine had separated at the water line, and fallen off into the tank. This is typical.
The anode came out easy enough with the use of an impact wrench. DON’T lean on it too hard. Just rattle it enough to loosen it, then go by hand from there. You could try it with a breaker bar or ratchet, but you might spin the tank before you break it loose. Fair warning.
Never mind my sweats hanging in the background, the point is the anode, or what little was left of it. Holy crap! If it weren’t for the string of 9 gauge in the middle, it would have fallen off long ago.
I stopped hitting it with the impact the second it began to spin on it’s own. I had to twist it back and forth to get it out, but out it came. A new one is a little over 3/4 ” in diameter. Imagine if I had rattled that for a while with the impact. I’d be trying to pull out a cork-screw.
Typically, the tube part of a dip-tube falls off and all of a sudden you have only a few minutes of hot water. What isn’t typical, is being able to fish the old tube out of the tank.
That black thing is a flashlight, and the white thing is the old tube coming out of the hole. I used a coat hanger with a hook, and some patience. Once I got the tube to the hole, I grabbed it with needle-nose pliers and pulled it out.
This took two tries, and it definitely does not need to be done, but hey.. I’m AR, so sue me. The old one was slimy, and flimsy, so I don’t know how it lasted this long, but I was happy to have it out of there.
Rinsing out the tank was a chore unto itself. I don’t have a picture of that part because I was “head down-ass up” throughout that phase, but the process was this:
- get two basins
completely remove the drain so the big chunks could flow out
- remove the water “outlet” from the top (it was near plugged anyways)
- get the garden hose into the basement
- tilt the tank over as far as possible using blocks under the legs
- use a flash light in one hole to see through the second hole so you can wash and rinse sediment toward the drain with the garden hose through the third. A garden nozzle is essential for this. You don’t need much water to “rinse” with.
- as the drain plugs up, use a piece of wire with a small hook to clear the hole
- rinse and repeat
This is what the colander caught. You can click on all these pictures for full size.
That effort took the majority of the day, and I didn’t get it all. There were still big chunks that wouldn’t break up, but meh… I got what I could. Move on.
About 10 pounds of calcium and lime deposits came out, and quite a bit of sand and sediment as well, which sat all around the edge of the tank base, decreasing the heating surface between the flame and the water.
Here is a nifty diagram I found on the interwebs.. the point being the base of your water tank is dome shaped and the crud collects at the edge until is is basically the chimney (labeled as draft diverter) doing the heating.
Note: the anode is not attached to the hot water outlet as it looks like above. It is separate piece.
With that done, it was time to put it back together.
The anode was easy enough. The inner hole in the tank (not the fitting) was super tight, but with some downward pressure and back and forth action, the rod popped through and began to slide down easy. Patience. Starting the threads by hand, I then got the breaker bar out. Good and tight was good enough. I used a bit of Teflon tape to seal it up. ** don’t believe you need to use pipe dope to create a connection to the tank for the anode to work. The water is the connection… duhhh**
The dip-tube had to be cut to length, which for my situation was about 36 inches. How a person would know this without the old one is beyond me, so I guess I’m glad I fished it out for measure. You certainly wouldn’t want to deposit ice cold water directly on the heating surface time over time. I guess I was about 8 inches away with that cut. Some Teflon tape, and good and tight was good enough.
In the morning, I grouted the tiles, washed them down, and carefully slid the tank back into place using a door mat as a softener under the tank feet. I cut some rubber “feet” to go under the metal ones of the tank, and tilted it foot by foot off of the mat and onto the rubbers.
And then there was this… #%$#^*%^((!@!%$*
Damn pilot light wouldn’t stay lit. After holding it down for too long, I rigged up this to heat it for 10 minutes, and still nothing.
I took the damn pilot tube and thermocouple out, sanded it, did this, did that, put it back in and still nothing. Oh fer *(^)*( sakes… but before loosing it completely (which rarely happens anymore) I tried an old trick. I tapped around the edges of the base of the thermocouple with the handle end of a small crescent wrench… et voila! It stayed lit. Turn it to ON. Back away!!!!
Sometimes things just get a little stuck and need a small rap with a weighted object to break ’em loose, and here it is like it never even happened.
The hot water this thing puts out is just like new now. Cass wanted me to turn it down… It has to be more efficient than it was, and I probably added another 10 years to the tank life just by changing the anode (which I didn’t know I ought to do prior to me looking into how to change the dip-tube).
The other nice thing about all this is, the basement is now completely finished. I will still mount the upstairs cupboards down here once I’ve built the new ones for upstairs, but the construction is now complete, and that means more to me than I probably let on.
Honestly, this was one of those jobs that I sort of thought would never get done.