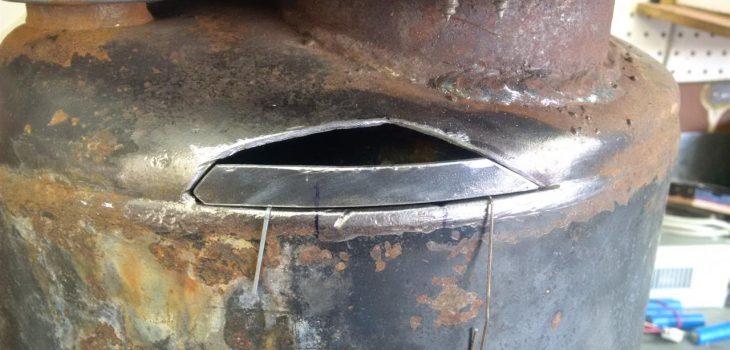
Red Whale 2.3: Beached
The Red Whale is done for the year, but not without a final success. * First, because I switched back to the classic editor, all the pictures are now clickable. If you want a better look at anything, just click on the picture. 🙂 *
The last endeavor at camping, and the horrendous return (as well as nearly getting stuck getting out of there due to the rains) discouraged us from trying it again until the problem(s) with the truck was found and resolved. This put a bit of a pinch on the rest of the summer, but luckily other accommodations became available, so we returned a few more times regardless.
In the meantime, the problems with the truck and trailer were put out of my mind completely until just recently, when I came across a B-pressure welder in my travels, as I knew I would eventually.
As a refresher, earlier in the year I had discovered my water heater tank had sprung a leak, so I pulled it out, patched up the outside of the trailer, and put the problem on the back-burner.
Well, now was later, and if you know me, once I have a grip on a solution, there is little that can get in the way of me finishing. First, my friend came by to see if it was something he could work with, and after a short glance agreed that it was nothing difficult, so I started to move forward immediately.
Over the summer I had kept an eye out for a propane tank, which I thought would provide the right gauge steel needed for the repair, and one did appear at the dumpster across the alley by the condominiums.
I had to remove the valve and then let it air out for several days before the propane stink wore off. I have a use for the valve, as a plug of sorts, as I don’t trust the regulator on the trailer to act as a stop if I ever remove a tank, and it’s just easier for testing purposes to hook up one tank and one tank valve instead of two tanks. I’m lazy, y’know. Anyways, once the valve was off, I cut off the valve protection on the top of the tank and used it as stock to fabricate my patch.
Prior to this, I had prepared the tank for a proper patch, cutting to the meat of the seam on the one side, and getting rid of as much rot as I could on the other. Unfortunately, I couldn’t get the mounting flange off the tank because it had press on fittings. This was a real drag, because it severely limited the ability to get in on it with a welding nozzle at the right angle. If it weren’t for that, the patch would have been much bigger, but these are the annoyances common to most field work. Conditions are rarely pristine, and “make do” often does the job just as well.
At first I thought I could get it with one piece, but the bend in the tank was just too sharp, so I decided it was easier to go with two pieces. One to build up the rim, and another cut to shape afterwards.
I thought that was a pretty good fit for a first piece, and the second had the shape needed, and could be cut wherever was needed.
I got it welded up, spent a wonderful day out in the sticks with his friends from B.C., and came home with a new set of problems… reassembly.
The gas valve is recessed, along with every other fitting within the mounting flange and the pressure relief valve broke off at the treads during removal. This had to be cut out with a hack saw blade and chisel, during which I nearly sliced my fingertip off as the mounting flange is nothing but sharp edges everywhere, etc… Needless to say, I wanted to go about reassembly with a little more caution, to save on blood loss, and ensure all could be installed without damage.
Chief among the issues was the gas valve, which needed a tool for installation, lest I slip (and slice) again with an over-sized monkey wrench. For this, I made a tool out of some C-channel I’ve had lying around for a few years, for God knows what reason.
The notch on the side (look at gas valve below) fits over the gas boss on the left side, the hole fit over the thermostat “dial”, and the nut welded to it fit a 24mm socket. This took some dreaming, but frankly, it worked like a charm.
I had to file the pressure relief valve so I could actually get a wrench on it, but that was minor compared with the torque that was needed to position the gas valve correctly. I had to strap the unit to the bench and grab my 1/2 inch breaker bar to get it done. Ugh. From there, the bleeder valve went in, and the rest of the flame/pilot assembly followed.
I don’t have any pictures of it, but the next steps were to re-wrap the insulation around the tank, tie it into place, and slip the steel case back over-top of the unit.
This was a miserable job – messy, with fiberglass dust and sharp edges – but once on, the water fittings could be mounted on the back, and the whole thing slid into place again in the trailer.
This was easier inside the trailer where a better idea of the positioning of the fittings, as well as the correct order to attach them was figured out. The propane line (top right) was a nasty bit of “make do” left over from the previous owner, but functional nonetheless. There you have it, sitting pretty, waiting for the next move.
So what next… Everything up until now had been in anticipation of a positive result, yet to date, I had not fired up this unit once in the last six years, so there were still some question marks hanging over the project, but lets get on with it, ok?
With the propane installed, I lit the stove to bring gas through the line faster. It still took a while to reach the pilot, which lit, but wouldn’t stay that way. I had a spare thermocouple sitting around (never thought I would write a sentence like that), and after some tweaks, had it in place with a nice flame at the ready. When I spun the gas valve to “On” it produced a nice flame in the chamber, so I knew the valve still worked.
To test the thermostat I finally had to fill the tank with water – and listen intently for a “hisssss” which never came – and see if it shut off once up to temperature. This was the nerve wracking part, checking for leaks, waiting for water to trickle out, but all went well, and hot water found it’s way out of the kitchen tap for the first time in years.
There is a saying… “I’ve had a lot of worries in my life, most of which never happened.” – Mark Twain – so I try not to worry, but anticipate. Same sh*% different pile.
With the test complete, it was time to install the tank permanently. I blew out all the lines, drained the tank, and then out it came so I could add putty tape around the mounting flange.
In my enthusiasm… I broke the little twist lock thingy that holds the cover closed… rats!
Not to worry, I made another from from ‘stuff’. It’s not perfect, but it’ll look good on the highway, and it was a lot faster than amazon….
While it was out, I also drained the remaining water from the tank which had caused the problem in the first place. The drain spigot was poorly positioned by design, which left an inch of water in the bottom of the tank regardless. I will have to come up with a solution for this by the end of next season, but that should be more than enough time. I already have a few thoughts.
So now, everything on the camper is back to working condition (except the front running lights, oh… and the canopy… ugh) and all that remains is whether or not I’ve solved the overheating problem with the truck.
Over the summer I used some chemical flush on the cooling system to clear any possible sediment that might have accumulated over the years. I got some out, but didn’t find anything worthy of note. Relatively easy to back-flush with a garden hose, my heater core works like a hot damn now, so I came away bettor off. I mean, it certainly didn’t hurt.
I also dropped the gas tank on the passenger side to inspect the lines to the sending unit and pickup inside the tank, but again found nothing untoward, so I didn’t bother with the other tank.
However, they are big tanks (90 L) without baffles in them, so running up a [Hairy] hill on a half full tank might have left a pickup dry long enough to suck air…. Once you have air in a line, it acts like vapor lock, and you’re hooped no matter the cause. Still, non-conclusive speculation though.
I guess I’ll never really know for sure, but tomorrow, weather permitting, I’ll run the Whale to the dump station to drain the holding tanks for winter. I’ll be watching the temperature gauge like a hawk, and when I get back, I’ll pull the spark plugs and look for a white plug. This would indicate coolant entering the piston, and could also be a cause of overheating. If that’s the case, then the hunt is on for a head gasket or cracked head. I hope I find nothing… which will leave me with the mystery, but I’d rather the mystery than a blown head gasket.