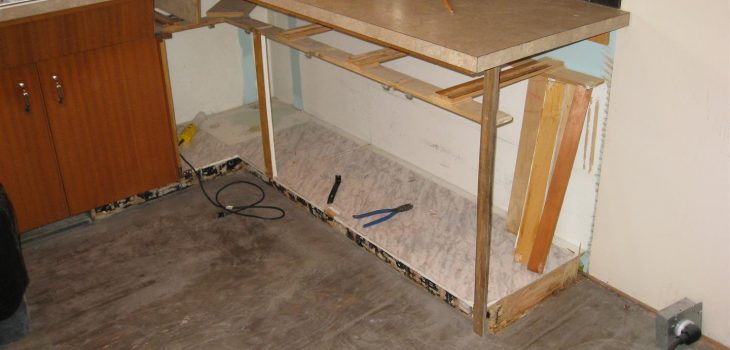
The Renos – Part II
With most of the evicted items out of the garage and spare room now, the rotation of room contents continued. Everything out, including the closet doors and shelf. Then up came the baseboards and the ugly carpet that covered a layer of original tiles.
Bedrooms
Having learned my lesson with the hallway tiles, I left these ones in place, and instead went over the whole floor, step by step, looking for squeaks. Everywhere I found one received 2 1/2″ screws, right through the tiles, until it was gone… and then a got few more for good measure.
From there, it was a process again, except I didn’t put in new baseboards, but refinished the old. Call me old fashioned, but I prefer actual wood over particle board. What I really enjoyed about this room, as well as the master, was getting rid of that God-awful wall-paper!
First I sprayed it down to soften it, and then peeled large sections off with a shit-eating grin! I know, wallpaper used to be a ‘thing’, but oh, it was ugly.
What didn’t come off got sprayed again, removed with a putty knife, and followed up with a thorough washing to get rid of the glue. Next steps were routine for all the rooms:
- Prep the walls
- Scrape and fill the ceiling
- Paint the walls (and closet shelf)
- Shoot and paint the ceiling
- Install the crown moulding
- Fill and paint it
- Install the flooring/baseboards
A fresh coat of Verathane had the baseboards looking new again. Windows are the next owners problem, as well as doors and frames if they wish.
I sure like the look of the crown moulding, and continue to be surprised at the difference it makes to the feel of each room it’s done to. While I was waiting for paint and mud to dry, I refreshed the baseboards and did the odd jobs each room required. If I recall correctly, rooms took under a week each to complete. Drop cloths in the hallway, and dust control were high priorities, as leveling the ceilings generated a ton of dust (and was the majority of the work).
The master bedroom and spare room followed suit, putting an end to more ugly wallpaper and carpet.
The ceiling fixtures and exterior plugs were sealed to prevent cold air coming through them. You would not believe how much of a draft could be felt!! If you were to add up all the holes I have plugged over the years, I am sure it would amount to a circle a foot across. Think about that for a second, if you please. $$$ Well, no more.
Kitchen
Yes, the kitchen. Every home owners nightmare renovation. Disruptive, never-ending, excruciating…. simply add your adjective (or expletive) and it will fit. Here, I discovered exactly the trauma a few misspoken words can cause, and those words were…
In this case it was finishing with “I’ll put in a dishwasher” that did me in. Now that it’s done, I’m happy, but here is the story, with a ‘before’ picture to remember what was.
Before I begin, it’s important to understand that I had already done a partial renovation in 2009, which was counter top, tiles and flooring. I was happy with the results, except for one thing. I had hand nailed the entire floor with a kajillion Ardox nails intending that the floor never squeak again, as it was awful noisy when I did it, and I just really really hate squeaky floors.
Ardox nails are twisted, with a square shank, and hold like a sonofabitch everywhere else, but not here. There are two types of nails in general. One is called “Bright”, which is just plain metal, and sometimes have a light oil on them to prevent rust, and the other is called “Coated”, which have a phosphorous powder on them to help them ‘stick’.
Well, I made the mistake of getting bright, thinking that they were Ardox anyways, and would hold like a bastard for that reason alone. I got about six months out of my work before the first squeaks began. First over by the stove, and then in front of the fridge, and then by the sink, and the door, etc… So I knew, that one day… I’d have to replace the whole floor again, but that this time it was going to be “Mike” nailed, and squeaks or not, it was NOT going to come out easy. And it didn’t.
The good news was that I had used a floating linoleum that wasn’t glued down anywhere. It was still in great shape, and could be folded up and removed just as it had been put in. There was a few bucks in my pocket!
With it out of the way, I began tearing apart the cabinets so the ceiling could be done, with the intent to run new cabinets straight to the ceiling to take advantage of the extra space.
Here, a support for the roof ridge had been poorly affixed, and had pushed down into the kitchen. This took some more gymnastics in the attic to positively support it (instead of side nail), then some mud, tape, and sanding until it couldn’t been seen. Years later, sign of this patch can’t be found, so I guess I got that right.
Once the ceiling was shot in and painted, the flow chart took a bit of a twist.
As I said, I liked the ’09 renovations, and didn’t want to lose the new counter top or tile work. I knew I would have to redesign the lower cabinets to make room for a dishwasher, but the tile work locked in the counter top, so that meant I was going to have to build the cabinets from the bottom up. Seeing as there was a lot I didn’t know about how these were put in place, I learned how it was done by tearing them apart.
Plans of saving part of the structure were quickly discarded, but before I could focus on that, the old underlay just had to be done.
Ugh!… In every picture above, you can place a little comic balloon over my head filled with expletives. This just sucked, and was a lesson in humble pie I’ll never forget. While I plugged away at this, I came up with a general plan to built the new cabinets, laying them out on the new sub-floor once installed.
While I was at it I properly placed the stove outlet into the wall. Old houses had their stoves hard wired to the house, so I had a stove plug in a box as a temporary solution. Much better.
Now it was time to turn my eye towards dismantling the rest of the cabinets.
The wasted space here was stunning, but I guess they had to give the drywaller his space too. I don’t know, but a better solution wasn’t too hard to come by.
With the underlay installed I began the layout.
Leveling down from marks above, I set out the bases, then decked them in. There was some mucking about with the heat register under the sink, and some work was put into plumbing the coming dishwasher. There is a space between the wall and the base for the drain and water line to be run, and on the other side you can already tell that the left cabinet will have way more space than before.
From there it was time to add gables, edge trim, and a first coat of Verathane on the deck.
Look at the space in there now! It was a pathetic waste before, fit only for rolls of wax paper and foil. I mean, c’mon! Anyways, shelving and interior gables were next, along with facing to mount doors to. Piece by piece, dry fitting was being done, and the little problems I couldn’t anticipate were solved.
Then, it was time for staining….
… followed by a proper test fitting, and a little gloating. At this point I had probably been in and out of the house a few hundred times, to the garage and back, fitting and refitting, SWEARING I would never do it this way again. I do remember pulling up a chair and sitting there for a while, just being happy with it.
The next phase was drawers, face plates, and doors. This was nice break from the back and forth from the house. I set up a jig of sorts to cut the dado in the drawer sides. For this I used Alder, a very light, workable wood ideal for the purpose. I know the jig is a mass of confusion, but it worked for me, heh heh… and the picture is so I can reproduce it if I ever have to. There’s no way I’ll remember.
Next came a rabbet for the base, followed by glue up. Say what you want, I was not going to muck about with a floating drawer bottom sitting in a dado. I needed full depth, and the drawers to remain square, which they have.
Once the drawers were stained they were basically usable, so in they went followed quickly by the lino, and once that was down, the dishwasher which had already arrived was installed. Though incomplete, this made a the kitchen usable again while work on the doors began.
I like the look of Maple, so that is what I went with. Trim was held in place with biscuits, and my little wedge jig worked like a charm. That picture above is Jig version 3.2 in case you thought I got it right the first time.
If you look close you can see a little bit of chip-out, which is damn near impossible to rid yourself of, but the miter is awesome, and once the finish was on, well…. I haven’t had any complaints. The pencil mark sanded out, by the way.
One by one they were put together until ready for a fitting. Here, I used the old style hinges, instead of the popular Euro-hinge. They only open to 90 degrees, and require a gable end to be mounted to in most cases. They may close nicely, and be all modern and ‘ohh ahh’, but being able to open a door all the way has a greater value to me. Cleaned up and polished, they look just fine.
I had to put together another jig to stain the doors, as I don’t have a sprayer or a booth to spray them in. The jig has nails top and bottom that fit into the holes for the hinge screws. They acted as a pivot so I could run a brush over all the surfaces without needing to touch the doors. It worked quite well, and the results were as good as could be expected short of an actual paint booth like big cabinet shops have.
From this point, all that remained for the cabinets was drawer fascia, and gable ends. I don’t know why I have no pictures of the fascia. It took a lot of problem solving to get the corners, and I had to give up on the plug I wanted to place beside the dishwasher, but the gable ends really brought the look together.
The problem here was a lack of handles on the gable end, which had to be glued on with 3M. The masking you see wasn’t NEARLY enough! That stuff gets everywhere and took some serious cleaning afterward. The handles worked like a charm, and were probably a little bit of over-kill, but they allowed me to control the piece fully while I placed the bottom. Contact cement on a big surface is a one shot deal. If it were to have touched accidentally before I had it sitting pretty, I would have been screwed. Oh, there’s probably a better way to do this, but it worked and, as I said, it brought the whole thing together.
Dishwasher Saga: The short version is that the one you see above was returned and replaced with the type below, which was also damaged during delivery, subsequently returned, and replaced again. Is it any wonder Sears went broke?
I got pretty tired of crawling in and out of this spot, but three dishwashers later it finally came in one piece, and that was that. Actually, it’s sort of roomy in there once you are in.
Once the first dishwasher was installed, and while stain was drying on the doors, it was time to focus on the rest of the room.
The ceiling was shot and painted some time ago to get that mess out of the way, and now the crown moulding could be done up until the transition point where it had to stop until the upper cabinets were completed.
That shot down the hallway is one of my favorite, but the little nightmare around the attic access was a hard won battle. Lots going on there, and it is still holding up. The only thing that has become an issue is the particle board expands and contracts more than regular wood does over the seasons, producing separations along the longer lengths in the winter. Painting it a different color (darker) would have help hide this, but you don’t know what you don’t know, y’know. If it weren’t for mistakes, I wouldn’t have learned a thing!
That pretty much does it for that round of renovations. The upper cabinets in the kitchen are still not done. I have to admit I’m at a bit of a designing bottleneck there, as I don’t simply want to reproduce what is already there, and other issues (basement reno) have come into play as well, so it is now affectionately called my bi-polar kitchen with Maple on the bottom and Mahogany on top.
The next year, the rear entrance got the same treatment – tiles, new sub-floor, ceiling, walls, and crown moulding, and a proper window was put into the back door. Another gaping hole was eliminated under the door sill there (OMG!! no wonder my feet were always cold) and the space was finished to the bottom of the stairs.
Little known to me at the time, but a basement renovation was on the horizon, which is an already written post from a while back, and was a major distraction when one simply wasn’t needed. But that’s life.